How could additive manufacturing replace traditional manufacturing
Share This Article!
The Authors – Kerry Stevenson, North Forge Co-chair Board Member and Founder of Fabbaloo and Teena Lee, North Forge Marketing and Events Specialist
Cover image: Complex 3D printed parts [Source: Shapeways]
__________
In December 2020, Shapeways‘ penned an article blog entitled “Will Additive Manufacturing Replace Conventional Manufacturing?” At the time, Kerry Stevenson, North Forge Board Vice-Chair and Founder at Fabbaloo, at first glance thought:
“Many people believed additive manufacturing can never replace traditional manufacturing. It’s too slow, too expensive, and too complicated.”
His interest was piqued, though, so he did some digging and thought, “Or is it?“
Fast forward a couple of years since the start of the pandemic to today: cracks in the supply chain have widened, causing detrimental production and shipping delays that have put a dent in the economy. As a result, entrepreneurs have had to pivot quickly to continue to meet current and expanding commercial and consumer demand and, at the same time, troubleshoot ways to work within a fractured supply chain.
Barriers To Additive Manufacturing (AM)
The barriers of using AM have evolved and is still a work in progress, Stevenson explains:
- “Speed: The production time per part is significantly higher with additive approaches, as some traditional purpose-built devices can produce 100,000s of units per day
- Cost: The cost per part is notably higher with additive, although the break-even line is slowly shifting over time
- Material Choice: The choice of materials for additive production is significantly lower than for traditional approaches.”
With Kerry’s 15+ years experience in AM, he sees that “the first two barriers, speed and cost, are the same thing. Consider the acquisition cost over, say, five years, of a production machine that produces 1M units per week vs a slower additive system that produces 25,000. The acquisition cost per produced part over those five years differs by a ratio of 40!”
Advantages Of Additive Manufacturing
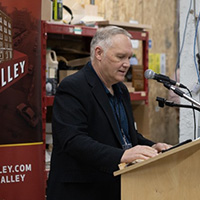
Kerry Stevenson at the FabLab 10th Anniversary in October 2021
And with those, you’d think there is no future. However, Kerry advises there are advantages of additive approaches:
- “Complexity: Objects of arbitrary complexity can be quickly produced, leading to post-production efficiencies and cost savings in some applications
- Flexibility: Production can start far faster as there is little to no setup time required, unlike traditional manufacturing.”
Future Shift To Additive Manufacturing
Will this equation ever change? Kerry feels it can happen in different ways:
“There’s first the apparent effect of technological progression. As time passes, we continually see more rapid additive solutions. A twelve-laser system works a lot faster than a two-laser system, or a higher-volume device can make more units per job, for example. Of course, those incremental changes will continue to pile up over the years, but 3D printers will not meet or even closely approach traditional manufacturing’s speed in my lifetime.
However, that speed increase will increasingly light up low-volume production business cases. Depending on the scenario, the break-even point will continue to rise. When the cost is the same, the flexibility advantage of additive will tip the decision balance.”
Kerry notes that other things might happen to alter the equation.
“One might be the surprising development of new forms of 3D printing processes that could lead to massive speed-ups in production. I can’t say what they might be because they haven’t happened yet. However, research continues worldwide, seeking new ways to make objects.
One promising approach is the volumetric 3D printing concept that several parties are developing in their labs. If it works and allows for the use of suitable materials, this technology could speed up production by perhaps 100x. That would move the break-even line far, far higher.”
Another factor that Kerry feels could increase additive approaches is not a technology at all but a behavioural effect, “today we are all accustomed to receiving parts in uniform designs and sizes, which was a solution to a need early in the industrial revolution, where hand-crafted parts were generally not interchangeable. Efficiency was gained by making parts in standard designs. Mass production approaches perfected this concept by doing it at scale.”
Kerry thought a lot about our need for uniform parts at all times. But, he questions, “what if consumers became accustomed to personalized “parts” for their needs?”
This effect might begin with 3D-printed shoes, for example. But having experienced customization in one product, consumers might expect the same in other products. A world full of consumers expecting customized products is a world that is just a few steps away from making most things in customized form.”
Kerry cannot say whether this reaction would occur, but “it’s something that we may see signs of in today’s production.”
There are also developments in the materials area where Kerry believes the breadth of material choice for use in AM will increase over time.
For example, 2022 may see the growth of feedstock filaments (different types of materials used to make 3D printed items) that could drive more applications across a wider net of industries.
Fabbaloo 2022 predictions from the article:
- increase in the use of AM techniques,
- increase in the number of powerful low-cost 3D printers hitting the market,
- stronger demand for larger build formats, functional materials, scaled post-processing, and full factory automation solutions,
- greater production consistency and yields from advanced adaptive machine learning and vision technologies,
- cost-effective and practical that covers a product life cycle,
- effective larger fabrication tool for planes, trains, vehicles, homes,
- effective for smaller fabrication such as atomic structures,
- convergence of exponential technologies.
The future is bright for additive manufacturing in how it can diversify and lift up our economy. It will be interesting and exciting to see which of those innovations pull ahead of the pack, redefine the scope of AM, and become commonplace in the future.
__________
Are you an additive or advanced manufacturing professional that sees a gap in the industry and has a solution that you’d like to flush out?
Have you worked with a manufacturing process and feel you have an innovative solution to streamline the process?
We would love to hear from you! Tell us about your idea (don’t worry if you don’t have the answers to all the questions yet), and the Programming Team will contact you to set up a meeting to chat about it.
If you’d like to see the advanced manufacturing equipment we have available at our FabLab, we invite you to register at our Meetup page for a tour.
Has the idea of a FabLab so close to home sparked an idea for an advanced manufacturing business? Become a FabLab member today to rapidly prototype your idea and help bring it to life.
Are you interested in building your own rural FabLab with the advice and guidance of North Forge? Contact Marney Stapley today to see how we can help.